Understanding What is Porosity in Welding: Causes and Solutions
Understanding What is Porosity in Welding: Causes and Solutions
Blog Article
Porosity in Welding: Identifying Common Issues and Implementing Ideal Practices for Avoidance
Porosity in welding is a pervasive issue that typically goes undetected until it creates considerable issues with the honesty of welds. In this discussion, we will discover the crucial factors contributing to porosity development, examine its damaging results on weld efficiency, and discuss the ideal practices that can be embraced to lessen porosity incident in welding processes.
Usual Sources Of Porosity
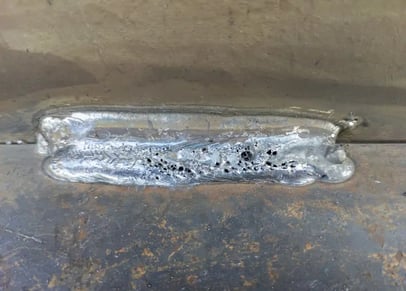
Another constant perpetrator behind porosity is the existence of pollutants externally of the base metal, such as oil, grease, or rust. When these impurities are not successfully removed before welding, they can evaporate and become caught in the weld, causing defects. Utilizing unclean or damp filler materials can present impurities right into the weld, contributing to porosity problems. To mitigate these typical reasons for porosity, comprehensive cleansing of base metals, appropriate securing gas choice, and adherence to optimum welding parameters are necessary techniques in achieving high-grade, porosity-free welds.
Influence of Porosity on Weld Quality

The existence of porosity in welding can significantly compromise the architectural integrity and mechanical residential properties of welded joints. Porosity develops spaces within the weld steel, deteriorating its general toughness and load-bearing capability.
Welds with high porosity levels have a tendency to show reduced effect toughness and lowered capacity to warp plastically prior to fracturing. Porosity can hinder the weld's capability to properly transmit forces, leading to premature weld failing and possible safety hazards in vital frameworks.
Finest Practices for Porosity Prevention
To enhance the architectural stability and high quality of bonded joints, what details measures can be executed to lessen the incident of porosity during the welding procedure? Making use of the correct welding technique for the specific product being bonded, such as readjusting the welding angle and weapon placement, can better stop porosity. Normal examination of welds and prompt remediation of any kind of issues identified throughout the welding procedure are crucial techniques to prevent porosity and create premium welds.
Value of Correct Welding Methods
Implementing proper welding strategies is vital in making sure the architectural integrity and top quality of welded joints, building upon the structure of efficient porosity prevention measures. Welding techniques straight affect the general stamina and longevity of the bonded structure. One key aspect of correct welding techniques is preserving the correct warmth input. Extreme warmth can lead to raised porosity due to the entrapment of gases in the weld swimming pool. On the other hand, inadequate heat may lead to incomplete combination, creating prospective powerlessness in the joint. Additionally, making use of the appropriate welding specifications, such as voltage, present, and travel rate, is critical Website for attaining sound welds with minimal porosity.
In addition, the option of welding procedure, whether it be MIG, TIG, or stick welding, should align with the details requirements of the task to make sure optimum outcomes. Correct cleansing and preparation of the base metal, along with choosing the best filler material, are additionally vital components of skillful welding methods. By adhering to these finest methods, welders can decrease the danger of porosity formation and produce top quality, structurally sound welds.

Examining and Quality Control Procedures
Examining procedures are vital to discover and prevent porosity in welding, making sure the stamina and sturdiness of the final product. Non-destructive testing techniques such as ultrasonic testing, navigate to these guys radiographic testing, and visual assessment are frequently utilized to identify potential flaws like porosity.
Performing pre-weld and post-weld assessments is also crucial in keeping top quality control criteria. Pre-weld assessments entail verifying the products, devices setups, and tidiness of the workspace to avoid contamination. Post-weld evaluations, on the other hand, analyze the last weld for any kind of issues, consisting of porosity, and verify that it fulfills specified standards. Implementing a comprehensive top quality control plan that includes complete testing procedures and inspections is critical to decreasing porosity issues and guaranteeing the overall quality of bonded joints.
Verdict
Finally, porosity in welding can be a common concern that influences the high quality of welds. By more tips here recognizing the common reasons for porosity and implementing ideal methods for avoidance, such as appropriate welding techniques and testing measures, welders can guarantee premium quality and trusted welds. It is essential to focus on prevention techniques to reduce the occurrence of porosity and preserve the honesty of welded structures.
Report this page